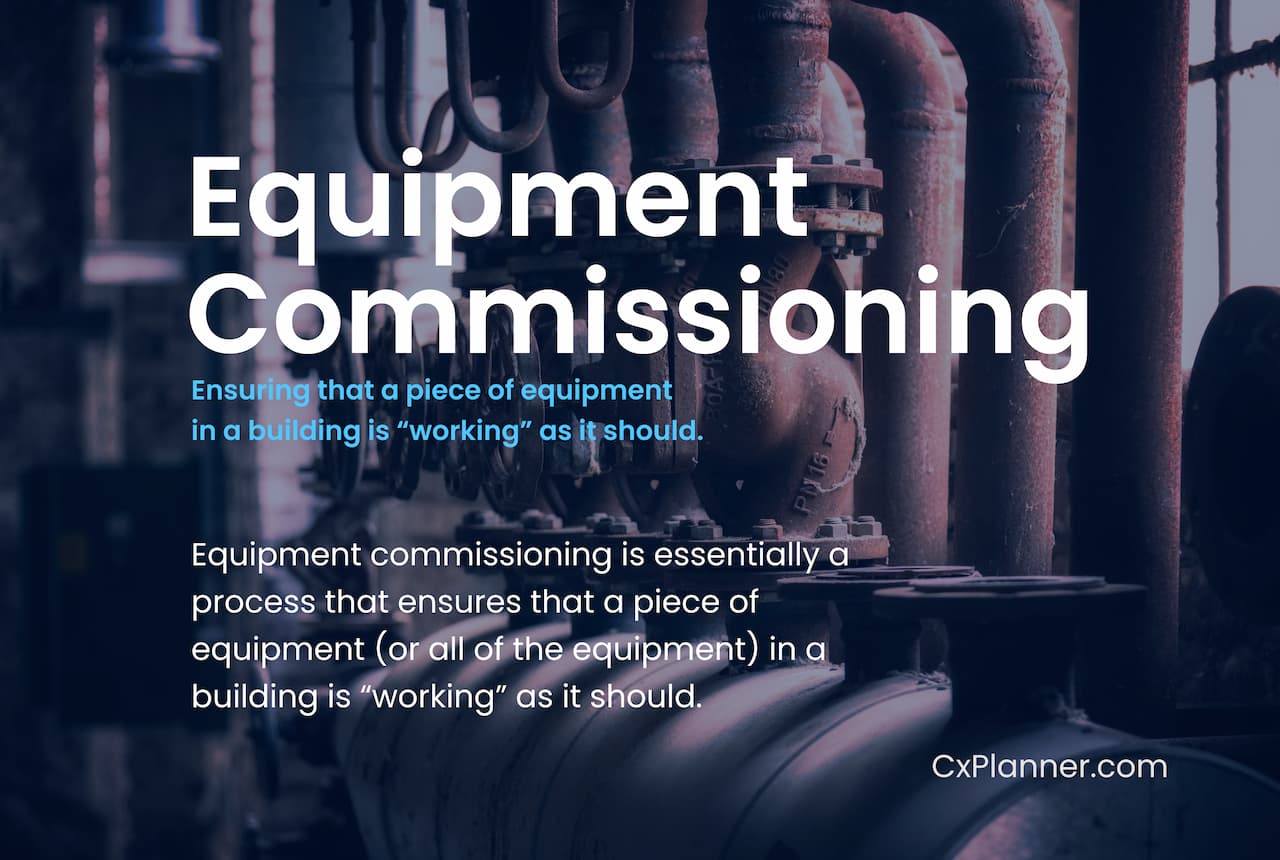
Table of content
Introduction to equipment commissioning
All of the systems and equipment in a building have a specific job to do. They have certain parameters they need to fulfill in terms of both code and owner's requirements—and new requirements are developing every day. For this reason, equipment commissioning should be as simple, as duplicatable, and as flexible as possible.
But what does commissioning equipment mean, and how does it work? How can the process of checking every system in a building be simple? This Ultimate Guide to Equipment Commissioning will explain all of that and more.
What is Equipment Commissioning?
Equipment commissioning is essentially a process that ensures that a piece of equipment (or all of the equipment) in a building is “working” as it should.
We use the term “working” here to describe several requirements that the equipment is tested against. Yes, the equipment must operate, but the commissioning process also ensures that it was designed, installed, functions, and performs properly, efficiently, and safely over time.
A commissioning team is responsible for this process. It develops a plan, executes the verification and testing, and then compiles important documents and reports throughout this process. Any issues with the equipment can be determined and corrected along the way. Finally, commissioning culminates and handover, at which point the equipment has passed all its requirements.
Which Types of Equipment Requires Commissioning?
Several types of building equipment should go through the commissioning process (also known as Cx). These systems include items such as:
- Air handlers (AHU)
- Cooling towers
- Boilers
- Electrical systems and components
- Plumbing systems and components
- Elevators
- Fire alarm and sprinkler systems
- Building controls
- Solar equipment
- Green energy systems
Essentially, any system that helps a building operate for its intended purpose should go through a process that verifies it meets the code and the owner's requirements.
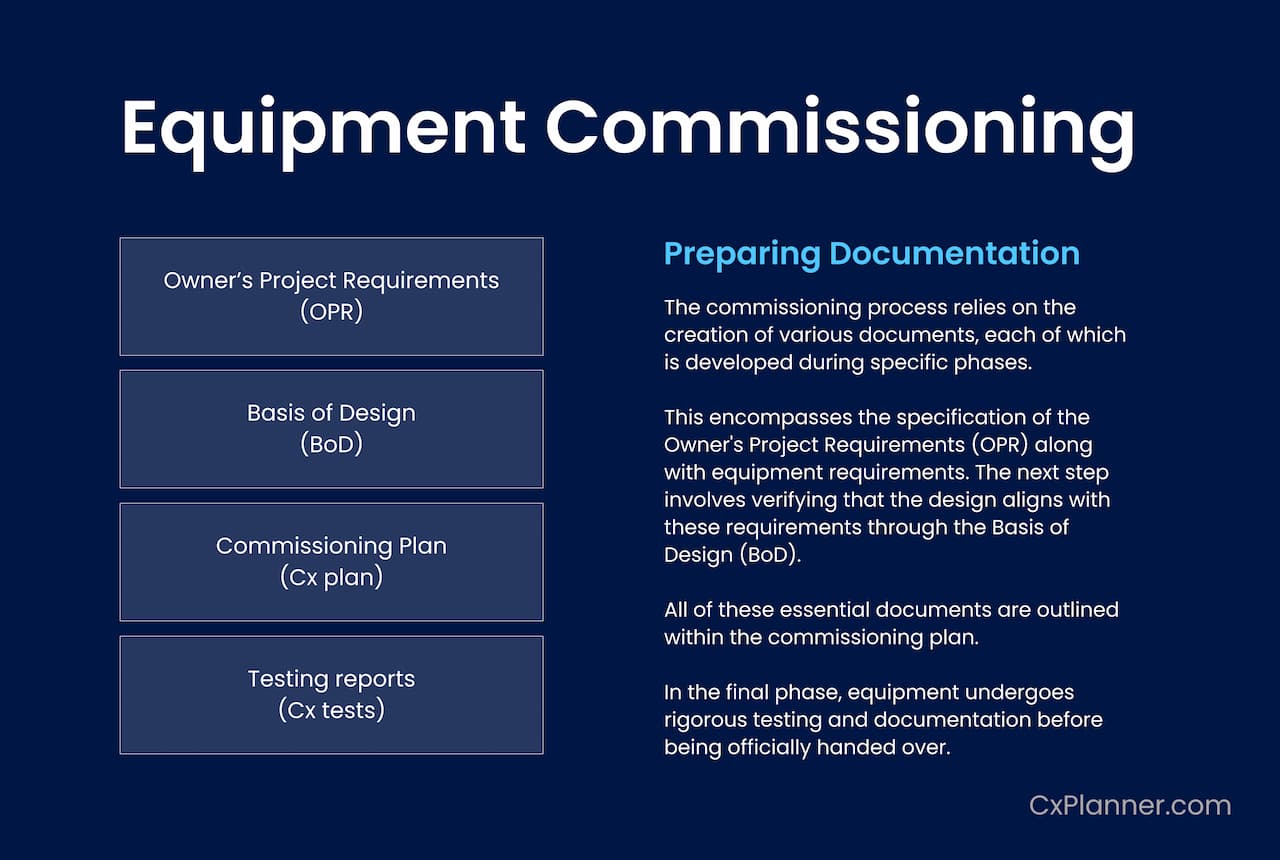
Best Practices for Successful Equipment Commissioning
Compared to the age-old construction industry, using the Cx process to ensure quality control and verify that systems meet requirements is relatively new. Only since buildings became increasingly complex did a systemized process become essential for quality control. The following are some of the best practices for a successful commissioning process.
Preparing Documentation
So much of the commissioning process relies on preparing documentation. Cx is a process that should begin at the preconstruction phase and continue through all of the phases of the project. Each phase throughout that process - pre-design, design, construction, and acceptance - has its documentation requirements.
There are several types of documents to prepare, based on the equipment being commissioned and the scale of the project. However, the following are always included:
- Owner's Project Requirements (OPR)
- Basis of Design (BoD)
- Commissioning Plan (Cx plan)
- Testing reports
- Roles and responsibilities
Ensuring Quality Control
The process of equipment commissioning is, at its core, a quality control and assurance activity. However, even the commissioning process requires quality control.
A Cx plan should detail all of the different aspects of the tests at each phase. It should also include who is responsible for those tests.
Employing systems that ensure the tests are carried out in order and sufficient detail will result in a high-quality Cx process. And, to take quality control further, assigning responsibilities and roles to each of those aspects of the process ensures that each team member is accountable and knows their responsibilities.
Communication and Collaboration
As with any multi-part project, commissioning is most efficient and effective when communication and collaboration are focus points. Depending on the equipment or the scale of the project, there could be dozens of people (hundreds, in some cases) working on commissioning teams.
Ensuring these team members have a platform with which they can share information means fewer holes in the communication chain and keeps everyone on the same page.
Common Challenges in Equipment Commissioning
There are a lot of moving parts on an equipment commissioning team. From actual moving parts in the machine to the different tests to all of the folks responsible for execution, a lot is going on. As such, there are some common challenges that commissioning authorities (known as CxA) and their teams face.
Dealing with Equipment Failures
Equipment can fail or simply not operate as expected during commissioning. Perhaps a sensor isn't responding properly, or some mechanisms are broken or assembled incorrectly. These items need to be sorted out, but it's not that simple.
First, the Cx process has to allow for equipment failure. The timeline and adjustments necessary have to be simple to make, and everyone the failure impacts needs to know. Also, the person who discovered the failure needs the ability to let everyone know what has occurred. With large-scale projects, this can be a lot to handle without the right platform.
Managing Time and Budget Constraints
Equipment commissioning can be an expensive and time-consuming process. Each phase of the project has requirements that need to be met and this might require large commissioning teams.
If these teams and their responsibilities aren't organized and scheduled effectively, the commissioning process can go from a quality control activity to a waste of resources.
Handling Unexpected Situations
The various layers of testing and verification throughout the equipment commissioning process are likely to uncover hidden challenges and situations. They're often completely unique from project to project, which makes them extremely difficult to plan for.
Without the ability to absorb a challenge into the timeline, determine a solution, and remain flexible, the Cx process gets sidelined. This means that not only are the owner's requirements unlikely to be met on time, but so are the ever-changing requirements that code enforcement and other Authorities Having Jurisdiction may demand in order for the equipment to operate.
The Impact of Technology on Equipment Commissioning
Just as buildings have become more complex since Cx became popular, the tools to complete the process have become more capable. Technology is making the process of equipment commissioning easier, more efficient, and more accurate than ever before.
Automation and Commissioning Software: A Game-Changer
When automation technology is the engine driving the commissioning process, the entire system becomes faster and more efficient. The Cx team can be more flexible, challenges are easier to handle, and communication becomes second nature.
- Customizable dashboards: Users can quickly and easily understand the status of the different aspects of the Cx project in real time. They can remove charts and diagrams they don't need and replace them with the data they'd prefer.
- Predefined templates: Rather than spending time developing spreadsheets for each aspect of a project, Commissioning software can provide predefined templates for each stage of the project. They can also be customized to meet the project's needs.
- Practical layouts and design: Rather than using complicated and exhausting spreadsheets, automation software can provide simplified, practical designs that make equipment commissioning easier. Technicians receive their assignments on mobile devices, and these assignments include the steps required for testing in a clean, easy-to-use format.
- User-friendly designs: Simplifying the onboarding process and getting entire teams up and running is a hallmark of excellent Cx software. These programs provide the platform for team members to walk through the testing process and communicate easily, ensuring everyone will use the program and keep all of the data up to date.
The Long-Term Benefits of Proper Equipment Commissioning
Equipment commissioning doesn't just benefit the construction phases. It also has long-term benefits that could impact the equipment for years to come. We have built CxPlanner to manage the commissioning with focus on these:
Ensuring Operational Efficiency
Equipment commissioning ensures that the systems in a building are running according to design and the project owner's requirements. The process ensures that the equipment is properly installed and operating as efficiently as it's designed to do. This makes long-term efficiency more consistent and predictable, and also offers a handy starting point for comparison should any design or building changes impact the systems down the road.
Enhancing Safety and Compliance
Part of the commissioning process involves testing each piece of equipment for safe operation and compliance with code requirements. All of the safety features of the equipment are tested, from sensors to handrails, ensuring that the commissioning team picks up on any potential violations before handover.
Extending Equipment Life and ROI
Building equipment is an investment, and building owners rightfully want to get as much for their money as they can. They want to ensure that the equipment will do what it's designed to do and extend its efficient usable life. A well-oiled Cx team with the right technology can all but ensure that this is the case during handover. These teams can peace of mind to the building owner that their equipment will run as long and offer as much return on the investment as possible.