Thesis evaluating CxPlanners performance (50% savings)
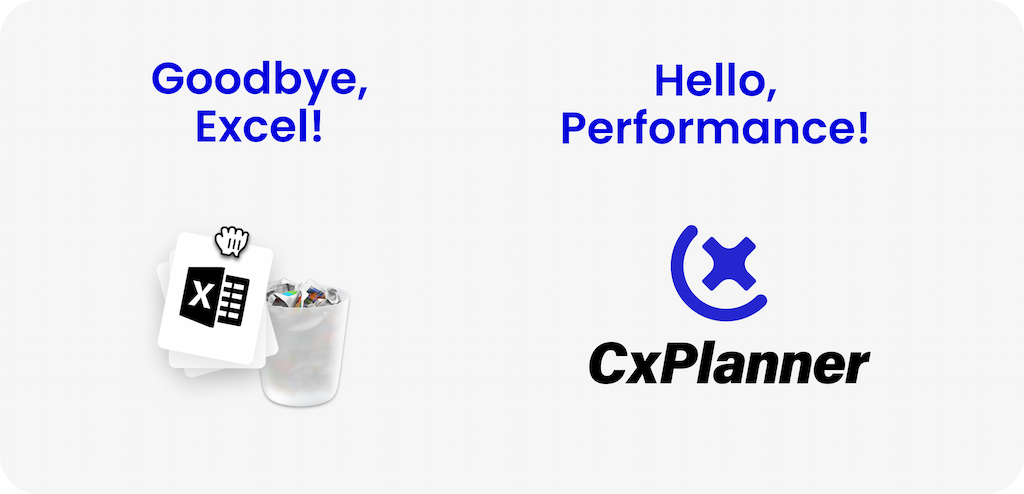
This article is a rewrite based on the Thesis of Matthijs Spijkers. All credit for the original content and research of this article goes to him. Matthijs has done an excellent job writing the thesis. For further information, please feel free to contact Matthijs Spijkers through his LinkedIn profile: Matthijs Spijkers on LinkedIn
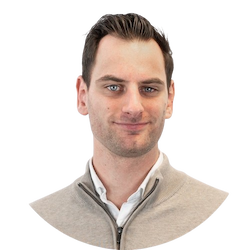
During my research, I quantified the time required, conducted a comparative analysis, and compared alternative solutions available in the market. Putting CxPlanner to the test in a real-life production environment showed that using CxPlanner resulted in a direct 50% saving in time spent performing MAT verifications, besides allowing for standardizing and streamlining workflows.
- Matthijs Spijkers
Introduction - setting the scene
This article serves as a summary of a thesis focused on performance improvement through the utilization of CxPlanner. The thesis, authored by Matthijs Spijkers, explores the efficacy of CxPlanner, a dedicated commissioning software solution, within the manufacturing industry. It provides an in-depth analysis of CxPlanner's impact on optimizing quality management processes, particularly in the context of the commissioning process.
Throughout this summary, we highlight key findings and insights derived from Matthijs's research, shedding light on the significant benefits CxPlanner offers in terms of time and cost savings, streamlined workflows, and enhanced quality management. It's essential to recognize Matthijs Spijkers's contributions to this evaluation, as his research forms the foundation of our analysis.
Highlights
- Implementing CxPlanner improved performance and saved +50% in labor work. This was proven by performing real-life tests with a 1-1 comparison with Excel.
- The platform worked seamlessly on all devices, making it easy to adopt by users, while still being compliant with cybersecurity standards such as ISO 27017, ISO 27018, and ISO 27001.
- The implementation also enabled standardization and streamlined workflows and processes to ensure continuous high-quality management across individuals and projects.
Evaluation and comparison of Cx software solutions
During the evaluation of CxPlanner, two distinct methodologies were employed. Firstly, by quantifying the time required and conducting a comparative analysis, it became feasible to ascertain the potential reduction in workload achievable through the utilization of CxPlanner.
Additionally, CxPlanner underwent comparison with alternative solutions available in the market, focusing on several functional requirements critical to the commissioning process.
The decision to continue with CxPlanner was informed by a comprehensive evaluation encompassing both time-based metrics and functional requirements assessment.
Time-based evaluation of Commissioning software
During the testing, a live test was conducted with CxPlanner to assess its potential time-saving capabilities. To replicate real-world conditions, two identical installations were selected for inspection. One engineer was tasked with assessing the quality using Excel for the first installation, while CxPlanner was utilized for the second. It's noteworthy that the engineer received only a brief 30-minute introduction to CxPlanner before beginning the evaluation, without any prior knowledge of the program.
The engineer's activities during both inspections were meticulously timed, and the tasks were categorized into three distinct phases:
- Preparation:
- Utilizing Excel involved copying and pasting data.
- With CxPlanner, the engineer selected the items requiring inspection.
- Execution:
- Checking the items on the respective checklists.
- Concluding Work:
- For Excel, finalizing the identified faults, creating a report, and uploading and saving the associated photos.
- With CxPlanner, the engineer simply pressed the "Generate report" button and saved the report to the local server.
Type | Total hours Excel |
Total hours CxPlanner |
Time saved in hours |
Time saved in % |
---|---|---|---|---|
Preparation work | 1 | 0.17 | 0.83 | 83.0% |
Execution | 3 | 2.5 | 0.50 | 16.7% |
Concluding work | 2 | 0.08 | 1.92 | 96.0% |
Total | 6 | 2.75 | 3.25 | 54.2% |
The results revealed a potential 50% reduction in the hours required for the commissioning process when using CxPlanner, translating to a significant cost reduction of up to €100,000 Euros annually in the most promising scenarios. Moreover, by extending the utilization of CxPlanner to Factory Acceptance Tests (FATs) and Site Acceptance Tests (SATs), this figure could soar to €200,000 Euros per year.
It's crucial to note that the substantial costs associated with rectifying errors at customer sites were not factored into this analysis, as they are not readily quantifiable. Nevertheless, it is plausible that these expenses amount to several hundreds of thousands of euros. The true extent of savings in these areas is anticipated to materialize after several months of integrating CxPlanner into operational workflows.
Evaluation of the functional requirements
In collaboration with multiple departments at the site, a comprehensive set of functional requirements was devised for software packages. These requirements are as follows:
- Project and Skid Level Analyses: The software must possess the capability to conduct analyses at both project and skid levels concerning quality checks performed. These analyses should be executable through a dashboard interface. The dashboard must offer a visual representation encompassing, at a minimum, the errors detected, approved quality points, and unavailable quality points. Furthermore, it should be adaptable per user to align with the specific data preferences of various managers.
- (Partial) Automation of MAT Checklists: The software should facilitate the (partial) automation of MAT (Manufacturing Acceptance Test) checklists to streamline preparation and validation processes, consequently reducing the time required for these tasks.
- Compatibility with Multiple Devices: It is imperative that the software is compatible with various types of devices, including Windows laptops, Android phones/tablets, Apple iPads/iPhones, or any other devices capable of operating within a secure environment compliant with ISO 27017, ISO 27018, and ISO 27001 standards.
- Management of Rejected Items: The software must allow for rejected items to be documented with a backlog detailing the reasons for non-approval. This documentation should be supplemented with text, images, or files as necessary. Additionally, each rejected item should be linked to an owner to ensure appropriate handling and accountability.
Management summary and conclusion
In essence, the recommendation for implementing CxPlanner revolves around several key points:
- Time and Cost Reduction: CxPlanner offers significant potential for reducing both the time and cost associated with executing the Manufacturing Acceptance Test (MAT) by partially automating the process.
- Stakeholder Empowerment: The software enables stakeholders to access essential project information, empowering them to effectively manage and control project quality. Additionally, it facilitates the acquisition of valuable data, enhancing project outcomes and results.
- Standardized Execution: CxPlanner ensures the consistent and clear execution of MATs, eliminating discrepancies in effectiveness across different executions. This standardized approach aims to detect more errors during MATs, potentially reducing the occurrence of errors at customer sites.
- Cost-Effective Error Detection: Identifying and rectifying errors during production, rather than at the customer's site, is inherently more cost-effective. By leveraging CxPlanner to enhance error detection during MATs, the likelihood of costly errors at customer sites can be significantly mitigated.
In summary, implementing CxPlanner not only streamlines MAT processes but also enhances project quality control, reduces error occurrence, and ultimately contributes to cost savings and improved customer satisfaction.
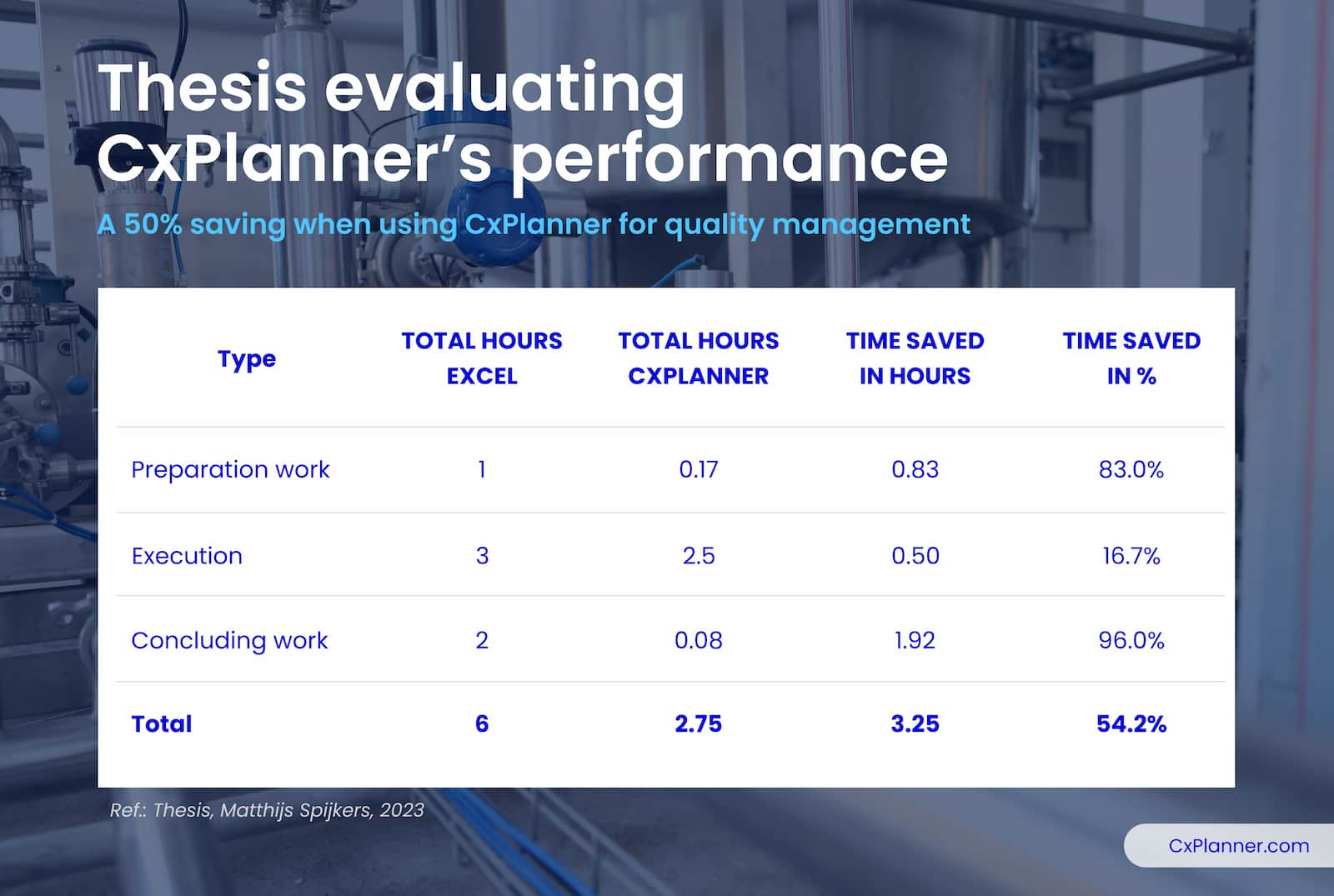