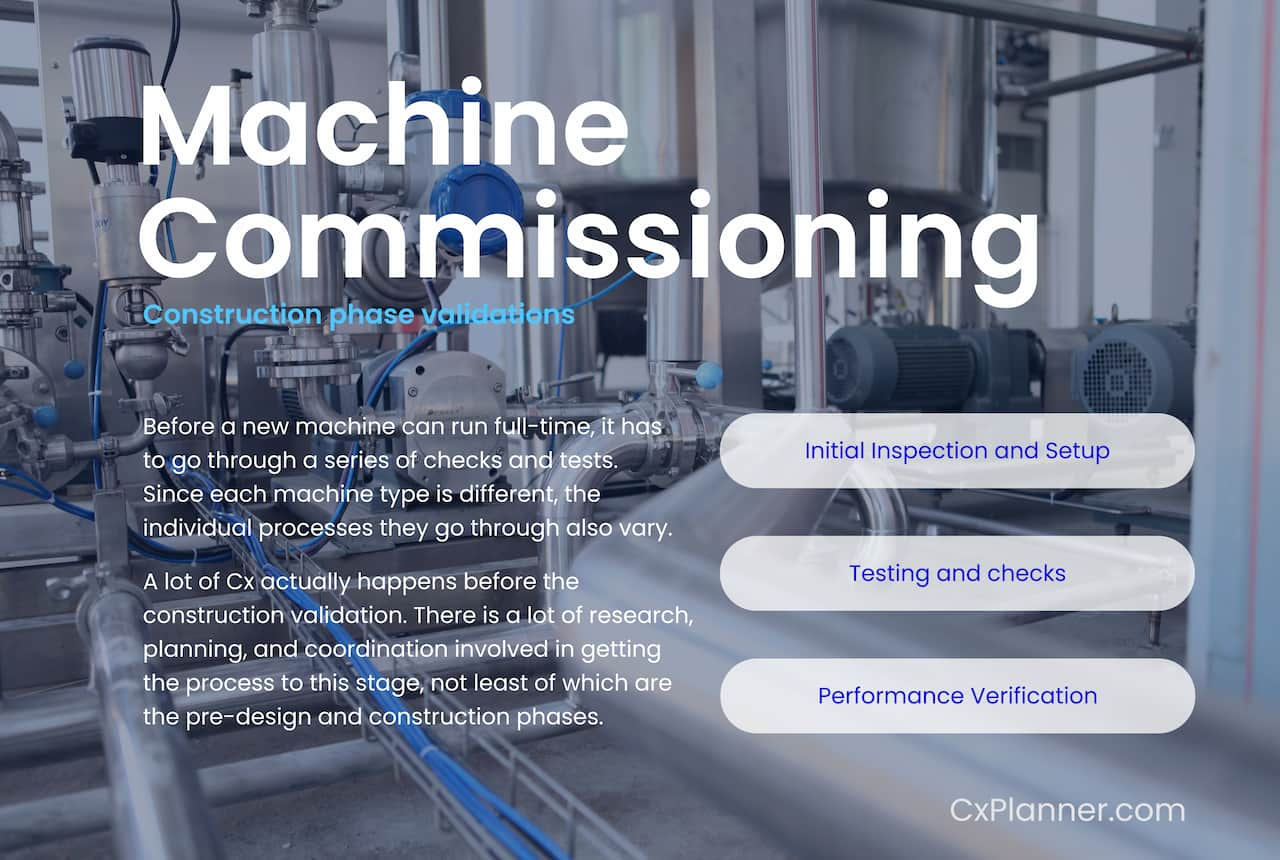
Table of content
What is Machine Commissioning?
When a new machine is constructed and integrated into a building, it has to be tested to ensure that it's working properly. Whether it's an air handler, an elevator, an escalator, a boiler, a chiller, or any other piece of building equipment, it needs to perform according to the owner's requirements and work flawlessly with the other systems in the building.
This is what the machine commissioning process accomplishes. The process starts at the pre-design stage and continues throughout the project, even into the operations stage. It consists of planning, testing, and certifying that all of the components and parameters associated with the machine are safe, efficient, predictable, and sustainable.
This dive into machine commissioning will explain more about the process, how it works, who's involved, and some of the challenges the commissioning team might experience.
What is a Machine and the Machine Directive?
The Machinery Directive is a global standard for everything related to a machine - from its design to how it operates, with a strong focus on safety. The Machinery Directive is a legal requirement in the EU and is also used in other parts of the world.
This directive has a clear definition of what a machine is:
- an assembly, fitted with or intended to be fitted with a drive system other than directly applied human or animal effort, consisting of linked parts or components, at least one of which moves, and which are joined together for a specific application,
A core element when we are talking about a machine is that it can often be a combination of multiple machines working together, and therefore, it is a machine in itself.
The aspect of machines working together as a whole is essential in the commissioning process because it is a part of the Integrated System Test/System Integration Test (IST/SIT).
The Machine Commissioning Process
Before a new machine can run full-time, it has to go through a series of checks and tests. Since each machine type is different, the individual processes they go through also vary. However, the following will explain an overview of the machine commissioning process (Cx) and what it involves.
Note: A lot of Cx actually happens before the following steps. There is a lot of research, planning, and coordination involved in getting the process to this stage, not least of which are the pre-design and construction phases. Most essential is the OPR and BOD.
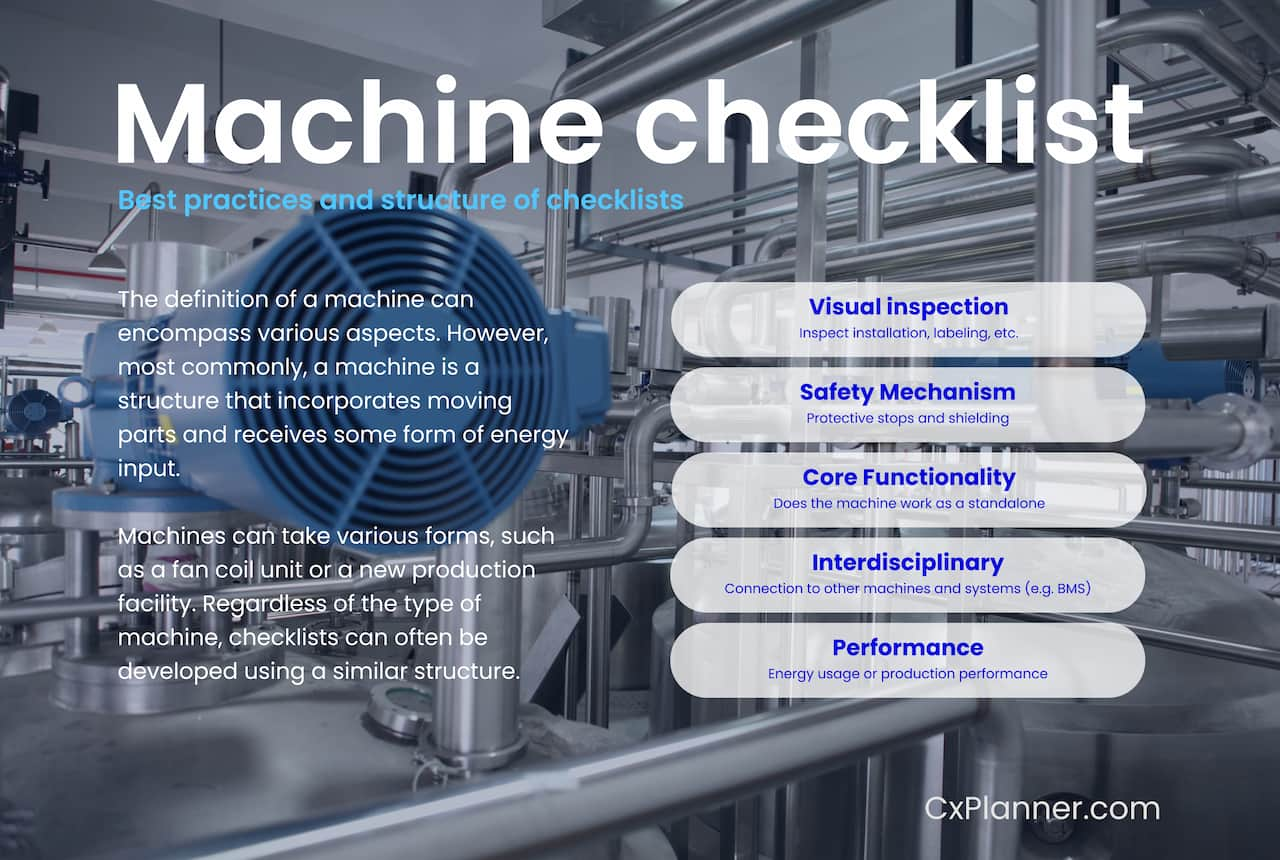
Initial Inspection and Setup
Machine commissioning might be a one-day process or take several, depending on the machine and its complexity and size. However, before commissioning can start, the machine requires an initial inspection and setup.
The initial inspection often means verifying that the individual cables, sensors, and mechanisms are installed properly. The Cx team will verify the hardware and components against the drawing or specifications, and ensure that the machine is safe and ready to test.
The test setup involves several moving parts. The Cx team will need to be in position at the various points throughout the building that the machine impacts. Also, the machine may need to be put into a “test mode” or the software updated for the test. Once these requirements are met, the Cx team can begin testing the machine for commissioning.
Testing
The testing process will vary based on the machine being commissioned. However, the test will often take place over a prescribed amount of time, and the machine will be cycled through its different functions to ensure that each function is working as according to the project requirements.
During the test, the members of the Cx team will be in position to verify that sensors, dampers, mechanisms, and software are working. They'll record pass, fail, or specific readings, depending on their tasks and the machine in question.
Performance Verification and Final Checks
The Cx team must do more than simply verify that the machine turns on and runs. The machine also needs to be tested for performance. The commissioning process is designed to identify issues but also verify that systems and machines are running safely and efficiently.
Performance verification may involve taking electrical readings, timing mechanism operation, and other measurable inspections. This helps the Cx team and owner verify that the machine will run as it's intended to for as long as possible.
The last part of the test (not necessarily the Cx process) is the final checks. This part of the process may involve a successful shutdown or reset, a final inspection of mechanisms and sensors, and even a restart to ensure that all mechanisms, sensors, contacts, and software meet the project requirements.
Technical documentation for a machine
An important part of the commissioning of a machine is to inspect and verify that the required documentation and submittals are present. Without them, you will not be able to test the machine or verify that the machine is safe to operate.
Often, the machine manufacturer will provide a compilation for the technical file that demonstrates the machine complies with relevant legislation. But be aware that the technical file for machinery combined with other machines must be updated by the integrator of the machine.
As a CxA you should check and ensure the following documenation is present:
- a general description of the machinery,
- the overall drawing of the machinery and drawings of the control circuits, as well as the pertinent descriptions and explanations necessary for understanding the operation of the machinery,
- full detailed drawings, accompanied by any calculation notes, test results, certificates, etc., required to check the conformity of the machinery with the essential health and safety requirements,
-
the documentation on risk assessment demonstrating the procedure followed, including:
- (i) a list of the essential health and safety requirements which apply to the machinery
- (ii) the description of the protective measures implemented to eliminate identified hazards or to reduce risks and, when appropriate, the indication of the residual risks associated with the machinery,
- the standards and other technical specifications used, indicating the essential health and safety requirements covered by these standards,
- any technical report giving the results of the tests carried out either by the manufacturer or by a body chosen by the manufacturer or his authorised representative,
Role of Commissioning Agents in Machine Commissioning
As with any type of commissioning, the commissioning agent (CxA) plays one of the most important roles in machine commissioning. This person is tasked with assembling and coordinating the efforts of the Cx team as well as planning the commissioning process.
Responsibilities and Expertise
Machine commissioning is typically a smaller, less complex process than commissioning the construction of an entire building. However, the CxA still has many responsibilities to handle.
The CxA is responsible for:
- Assembling the machine commissioning team, including any contractors, subcontractors, or maintenance personnel that need to be involved.
- Determining the scope of the machine commissioning project, including all of the sensors, mechanisms, functions, and legal requirements involved.
- Identifying the owner's project requirements (OPR), which provides the basis for the entire Cx process.
- Assembling the blueprint and testing procedure for commissioning the machine.
- Reviewing commissioning documents and drawings to identify issues early in the design and construction process.
- Preparing the commissioning test for handover.
- Performing ongoing commissioning testing per the plan.
When it comes to putting these commissioning projects together for multiple types of machines, a CxA has to have plenty of experience in the mechanical world. They need to know what to look for, how to read and understand schematics and be very well-versed in what it takes to identify the owner's project requirements.
Machine commissioning software can make this entire process easier, though. With the use of CxPlanner, CxAs can promote communication between the different Cx team members, as well as utilize it as a helpful platform for document storage and report generation. Also, an experienced CxA can leverage their knowledge by putting together a simple, easily understood plan through which every team member receives their tasks.
Collaboration with Machine Operators and Technicians
It is essential, if possible, to include the Operators and Technicians in the specification process for the testing of the machine. These are the people who will be operating the machine on a daily basis, and therefore, they have a lot of knowledge about the actucal use cases for the machine.
This knowledge can be used to ensure that the machine is tested in a way that is relevant for the actual use of the machine. You should develop the checklists and test scripts together with the Operators and Technicians. If possible, you should develop the test scripts for performance validation to be reusalbe for the daily operation of the machine. By doing this, you will ensure that the machine can be continously tested during the maintenance.
Common Challenges in Machine Commissioning
A machine is a combination of many moving parts that must work together. This also means that there are many different stakeholders involved in the commissioning of a machine.
Not proper installation or mounting
A machine is designed at a factory, but it is installed and mounted at the construction site. This means that the machine can be installed and mounted in a way that is not according to the design.
Wrongfully installed or mounted machines can cause a lot of problems and can be very expensive to fix. The errors can range widely, from the machine not being able to operate, to the machine not being able to operate safely, or generating a lot of noise due to vibrations.
If the machine is wrongfully installed, resulting in vibrations, that can cause problems for the machine but also for the area where the machine is mounted. The lifetime of the machine itself can be reduced, and the vibrations can also cause problems for the building or structure where the machine is mounted.
It is generally good practice for the Cx team to inspect and participate in a "first installation" of the machine. This will ensure that the machine is installed according to the design. If that is not possible, you should prepare a QA/QC checklist for the machine provider which documents it.
Integrations with other machines
The number one challenge in machine commissioning is the integration with other machines. A machine is often not a standalone machine but is integrated with other machines. The integration can as "simple" as a connection to the building management system (BMS), or it can be a more complex integration with other machines.
Integrating the machine with other machines can be a challenge because the machine is often designed and tested in a factory and then installed at the construction site. This means that the machine is not tested in the environment where it will be used. In addition to the physical environment, multiple different persons and companies are involved in the installation and commissioning of the machine.
A good practice is to develop detailed test scripts and specifications early in the project, specifying exactly how the machine should work and how the integrations will be tested. These will serve as design principles for the different parties, and everyone will be aware of how the testing will be performed.
Technology's Role in Machine Commissioning
The machines being commissioned are often high-dollar pieces of technology that make buildings function better and more efficiently. It would only make sense that introducing new technology would also improve Cx.
Benefits of Commissioning Software
Commissioning is a relatively new process, but until recently, it's been rather low-tech. The introduction of software designed for commissioning can streamline the process and help Cx teams achieve more in less time with greater accuracy.
The following are some of the biggest benefits of commissioning software:
- Real-time tracking allows CxAs, owners, and their teams to quickly identify exactly where the Cx project is in the process. Updates are instantly reflected across all user interfaces, keeping everyone on track.
- Clear, actionable plans that make all of the tasks associated with the Cx process easy to understand and record results. Checklists and procedure templates save time and ensure the process is performed correctly.
- Deficiency tracking allows the Cx team to identify and track the status of issues found during Cx.
- Simplified document management allows the CxA to keep all of the critical drawings, reports, and other documents in one place. Wide-spread access to all of these drawings can save time for the team members who need them, as well.
- Digitally-based recording and reports do away with Excel spreadsheets and pen-and-paper recording. Also, commissioning software can handle any editing automatically rather than performing manual edits of test results.
- Commissioning software is flexible enough to handle any commissioning project. This makes the setup and use of the software repeatable and streamlined.
- Simplified turnover package preparation makes it easier to package important documentation and reports and provide them to the owner. This means less work without sacrificing thoroughness or quality.