The Cost of Cutting Corners: Why Quality Matters in Construction
contains poor quality
due to poor quality
- Analysis of the poor-quality in building elements
- Poor quality can be found in all areas
- The problems are present in all the phases of the project process
- What can poor quality do on a construction project
- The indirect implications of bad quality
- How to solve poor quality with the right tools
- The commissioning process to verify and test
- Software for quality management
💰 Analysis of the poor-quality in building elements
A new research paper: "Analysis of the poor-quality in building elements: providers’ perspectives", delves into the issue of poor quality in the construction industry - and there's a lot of it!
The research used a survey method, where site operatives were asked to rate the frequency of variables within poor quality in 25 building elements and components. The survey was conducted on a five-point "Likert scale", with results showing that poor quality occurred in more than 80% of building projects. Additionally, the data revealed that approximately 40% of the cost of a building project is attributed to poor quality - almost half of it's cost.
contains poor quality
😒 Poor quality can be found in all areas
This research provides insight into the issue of poor quality in the construction industry. It highlights the importance of quality control and emphasizes the need for better anticipation and management of processes and tools to avoid poor quality in building projects.
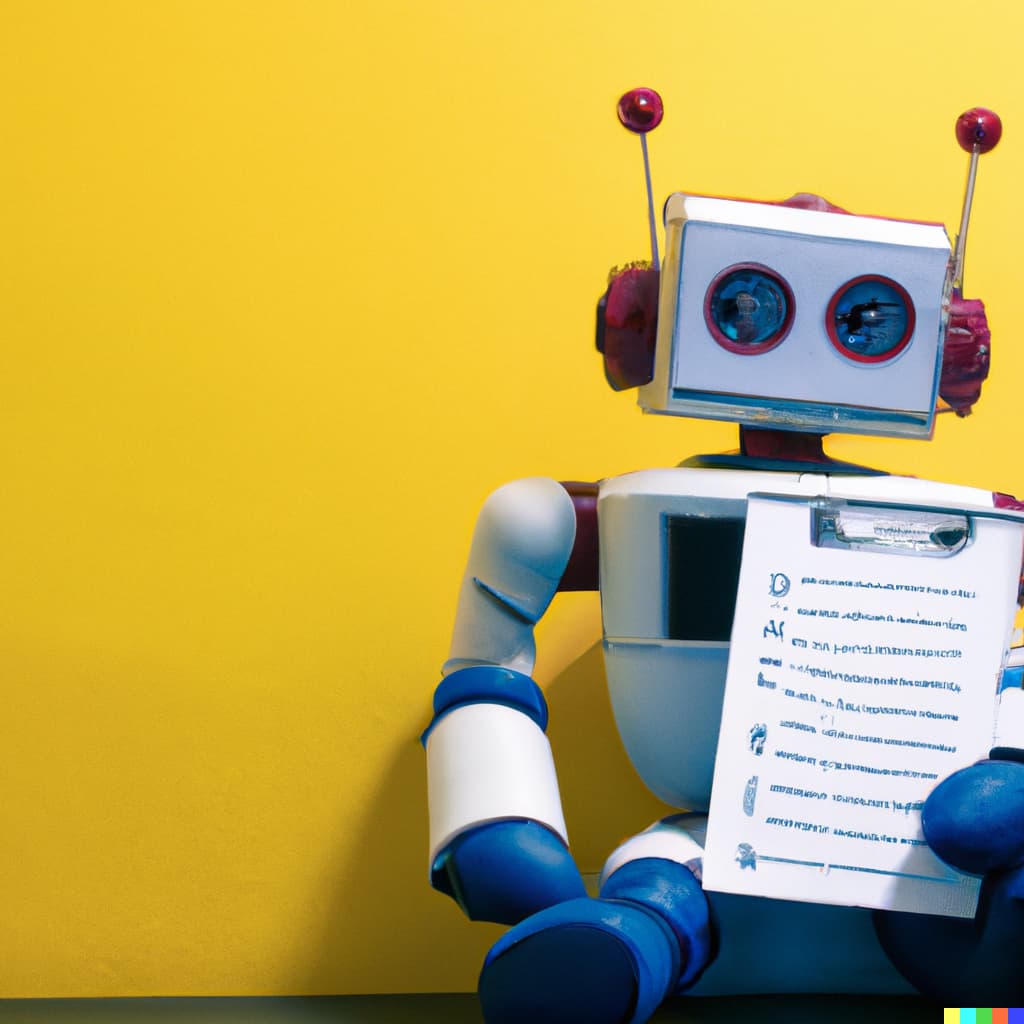
😬 The problems are present in all the phases of the project process
The study also found that the main cause of poor quality was attributed to a lack of proper supervision and inspection, as well as a lack of communication among the construction team. This highlights the importance of integration between disciplines and clear communication.
Another key finding from the research was that the majority of respondents believed that poor quality could be avoided or stopped by using good quality management processes and verification tools.
The research paper provides a valuable contribution to the understanding of poor quality in the construction industry. It highlights the importance of quality management, the role of good communication, and the impact of poor quality on the longevity of a building.
💲 What can poor quality do on a construction projec
Poor quality in building projects can result in significant extra costs, both in terms of time and money. The research paper states that poor quality can increase the cost of a building by up to more than 50% and can delay a project by up to 50%.
One of the main causes of extra cost is the need for repairs and rework. Poor quality materials and construction methods can result in defects and malfunctions, which need to be fixed. This can lead to additional labor costs, as well as the cost of replacement materials.
In addition to repairs and rework, poor quality can also lead to increased maintenance costs. A building that is not constructed to the required standards will require more frequent maintenance and repairs over its lifespan. This can add up over time and result in significant additional costs.
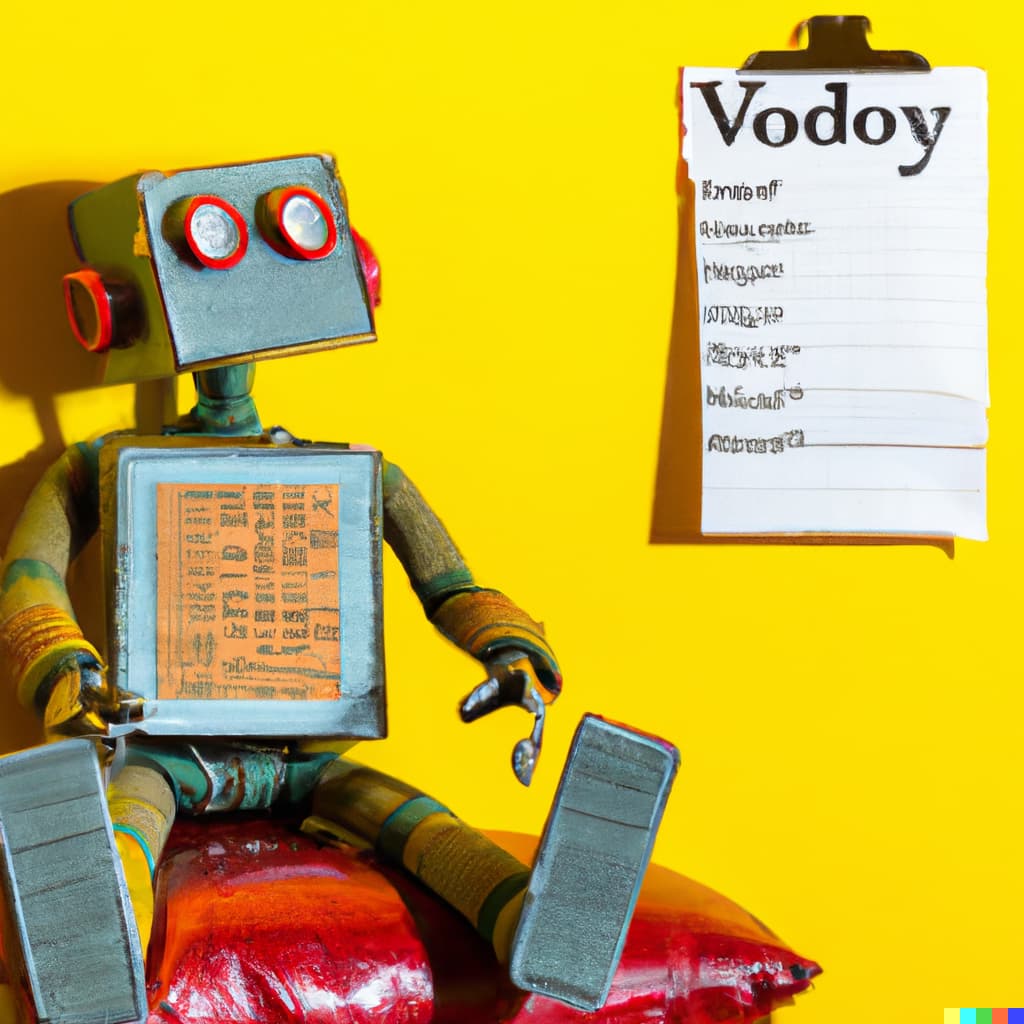
💬 The indirect implications of bad quality
Poor quality can also lead to legal issues and disputes, which can result in further financial costs. For example, if a building is not constructed to the required standards, the owner or occupants may be able to claim compensation or take legal action.
Finally, poor quality can also lead to a loss of reputation and credibility for the construction company. This can result in a loss of future business and revenue.
In conclusion, poor quality in building projects can result in significant extra costs, both in terms of time and money. It is important to prioritize quality in the construction process in order to avoid these extra costs and ensure that projects are completed on time and within budget.
✅ The commissioning process to verify and test
Another important aspect of quality management is the use of commissioning process, which is a quality-focused process that involves the verification and documentation of systems and equipment to ensure they are designed, installed, tested, and maintained to meet the owner's project requirements.
This process is particularly important for mechanical, electrical, plumbing, and fire protection systems, as these systems are essential for the proper functioning of a building.
Commissioning has multiple times been proven to be cost effective and have a short payback time. E. Mills has in 2009 and 2018 published studies showing that using the commissioning process on new construction and existing construction results in major economical benefits.
🏆 Software for quality management
Another solution to improve quality management is the use of tools and software solutions. And we have an idea for that 😁 ! CxPlanner! Using CxPlanner will help you to manage the commissioning processes and quality control activities by providing a central location for all project-related information, including documents, plans, and test results.
In conclusion, good quality management is crucial in preventing poor quality in building projects. By ensuring the contractor performs correct quality assurance, and that a commissioning process is implemented, and by using tools and software solutions such as CxPlanner we can in many cases mitigate the problems resulting in poor quality.
Only the ones who can manage quality efficiently will be part of the tomorrow