Improving Building Performance through Technical Monitoring and Commissioning
- Improving Building Performance
- Why are there so many issues on construction projects?
- Is there a solution for fixing the performance gap?
- The concept of Technical Monitoring
- The concept of the Commissioning Process
- Getting started with Cx and TMon
- Management system for Cx and TMon
- Want to learn more about Cx and TMon?
Improving Building Performance through Technical Monitoring and Commissioning
Poor quality is everywhere, but in recent years we have seen an increase of issues in the construction industry. And that is called the Performance Gap.
REHVA Guidebook no. 29 is a fantastic read on the problem and solutions within the field of quality management.
This blog post summaries the concepts and puts additional thoughts on them for professionals.
Why are there so many issues on construction projects?
New projects often include innovative technology for heating, cooling and air conditioning. But these new technologies increase the complexity and are a huge challenge for everyone - ranging from the design team to the operations staff.
The performance gap puts pressure on margins for everyone.
Even though the new technology should help us, it often results in buildings that do not perform as intended. And that can be very costly.
Not only does the building not perform as intended, the cost increases in the design and construction phase, and then later on in the operations phase, the costs are also higher than expected.
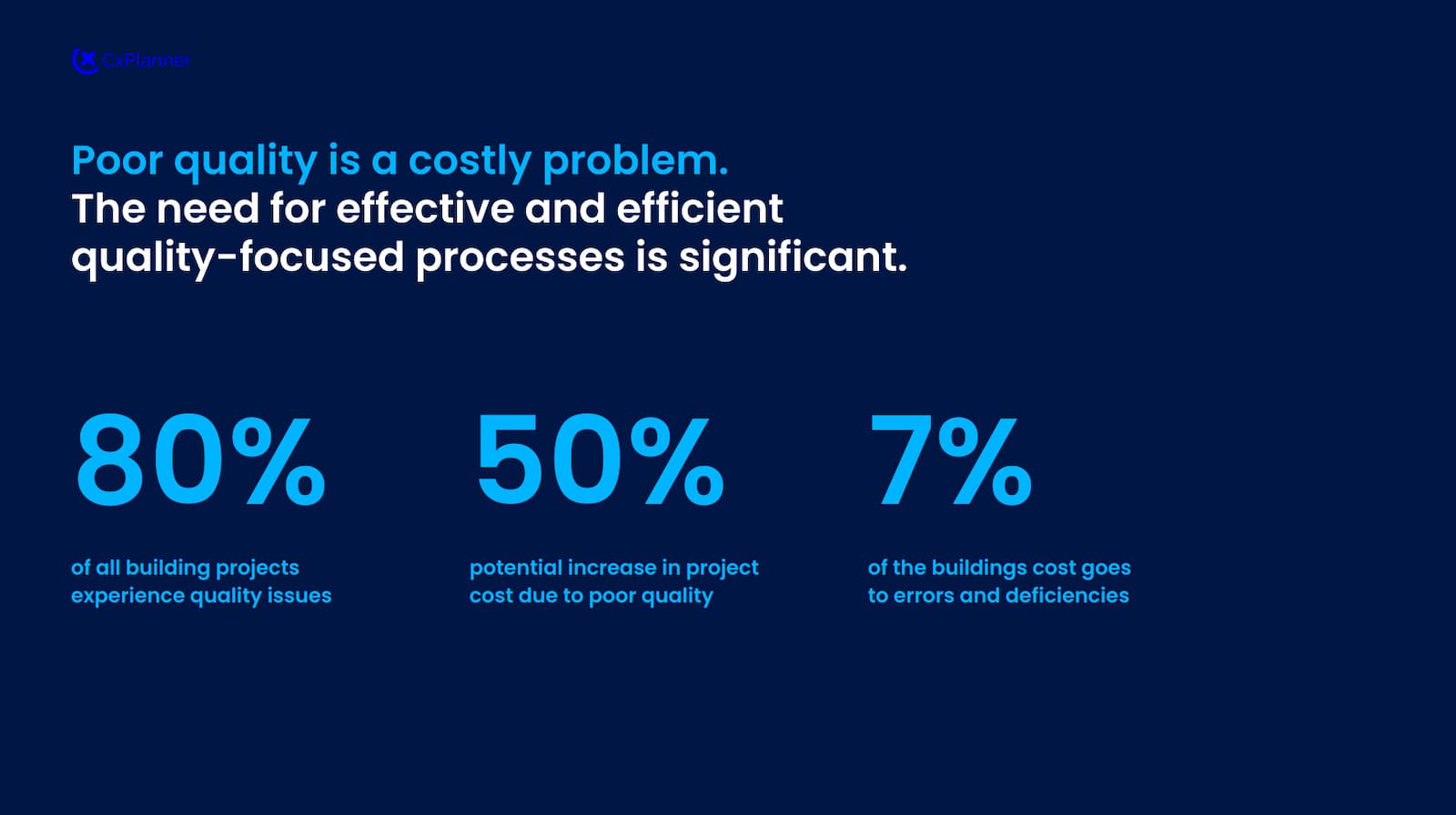
Is there a solution for fixing the performance gap?
To overcome and fix these kinds of problems real “Quality Management” is needed.
As stated in REHVA Guidebook no. 29, over the last years two solutions have evolved to be reliable quality management systems: Technical Monitoring (TMon) and the Commissioning Process (Cx).
Even though the guidebook makes a clear distinction between these two, in the practice of performing them, there are multiple overlappings.
What is Technical Monitoring
“Technical Monitoring (TMon) applies procedures to compare measured values from building operation versus design target values providing a transparent result to the owner. TMon can predominantly be carried out digitally.”
In short, it is a process to establish some specific activities, which during the building's operations phase continuously verifies that the building's performance complies with the requirements.
What is the Commissioning Process
Commissioning is a quality management process which verifies and documents that a construction project fulfils the owners requirements. The process is started in the project's idea-phase and continuous throughout the whole project and also into the operations phase.
What is the difference between Technical Monitoring and Commissioning
Generally speaking, the commissioning process can include technical monitoring, since the Cx process continues into the operation phase. Another aspect is “On-going commissioning”, where the Cx process is used to verify the building's performance during the operations phase.
Within the guidebook no. 29 there is a more distinct line between the two terms/activities, as the Technical Monitoring is seen as an independent activity and art.
The Cx process is a larger and more complex process than Technical Monitoring and requires more and high-level expert expertise.
The concept of Technical Monitoring
When working with Technical Monitoring there are 4 essential elements to focus on:
Category | Description |
---|---|
Target Values | These values define the requirements and establish the baseline. |
Measure Values | These values are what there’s measured manually or through e.g. a BMS system. |
Evaluation Procedures | How to check and verify that the Measured Values are in compliance with the Target Values. |
Actions | How to take action on the outcome of the Evaluation Procedure. That can either be when there’s a difference between the target and measured value, or if there’s a goal to continuously improve the building's performance. |
The concept of the Commissioning Process
While TMon consists of 4 main elements, the commissioning process is much more complex.
Commissioning is often seen as a testing process, but since it is started during the idea-phase, it has activities and tools for each of the project’s phases. A simple overview can be seen below, but for more details read this article or view the video.
Idea phaseDuring this phase the commissioning specification is developed. That includes the Owner's Project Requirements (OPR), which is the “target values” that are measured during the whole project.
Furthermore it is also in this phase that the initial commissioning plan is written that defines the scope of the commissioning activities.
Design phasesIn the design phases the drawings and specifications are developed. The commissioning team will manage the Basis of Design (BOD) where the designers verify that the design complies with the OPR.
The Cx-team will also perform design reviews.
Construction and handoverDuring the construction phase the Cx-team will verify that systems and equipment work as intended with a detailed testing plan. This testing plan involves FAT, SAT and SIT tests.
At the end of the project the commissioning process ensures that the documentation is handed over to the owner; and potential on-going commissioning is started.
Getting started with Cx and TMon
Every project is different, and so it is important to be very clear on the scope and detail level. Some factors to include is:
Factors | Description |
---|---|
Complexity of Building Systems | Residential buildings typically have simple systems, while laboratories have intricate and interconnected ones. |
Contractual Setup | If you, as the building owner, hire different engineers and contractors, paying attention to system interfaces is crucial. Alternatively, if you opt for a single contractor for engineering and construction (turnkey contractor), precise objectives and testing procedures should be clearly specified in the contract. |
Building Owner's Competence and Capacities | Building owners with extensive experience and large staff may have a better grasp of project quality, whereas those with limited experience, like one-time house builders, may require strong Cx support. |
Market Situation for Engineering and Construction Services | Busy engineers and contractors may be prone to providing incomplete or subpar services due to high project volumes. |
Buyer or Tenant Expectations | Some future tenants or buyers may have higher expectations regarding indoor environmental qualities, energy consumption, or maintainability, necessitating rigorous proof of quality. |
Management system for Cx and TMon
Essential for both commissioning and technical monitoring is that it is complex activities that can have a very big (positive) impact on the construction costs and performance.
It is not possible to manage any of these with legacy solutions such as Excel and Pen&Paper. You will not be able to manage the activities in an efficient way and keep track of everything.
Often these processes include numerous involved parties, where you need a secure and valid history of everything that happens, and a digital way to manage the data collection.
Want to learn more about Cx and TMon?
You are always welcome to contact us, and we can give you a crash-course in how you can implement it. That includes a short assessment and a direct recommendation on how you can get started.
You can also visit REHVA and download a full copy of the guidebook no. 29.